Case Study: Optimise Inventory Management in the Energy Industry
Industry:
Energy
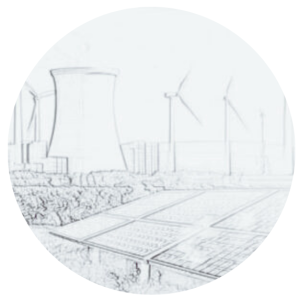
Project Summary
The client, a world-leading energy and infrastructure provider, decided to restructure their inventory operations in order to improve efficiency, simply their supply chain and maximise profit.
As part of this restructuring process, the client needed to reconfigure and combine various specialist stores into a single, centralised function to be managed by a dedicated third-party partner based on-site.
This transition to an ‘everything under one roof’ approach presented numerous challenges. The main issue to solve was to ensure continued adherence to British Standards in respect of quality and dimensions.
Method
As long-standing supplier to the procurement management and quality department, D.P. Fasteners was recommended internally as a potential procurement partner for the retail branch.
We assessed the needs of the new centralised function and determined precise specifications for the necessary parts as well as the optimal quantities to meet client production targets.
To ensure each fastener adhered to relevant quality and safety standards, whether that be British Standards or ISO and DIN standards, we structured and synthesised a variety of data.
Result
A resounding success
The fundamental aspects of the project were delivered as planned: we sourced the requisite parts within an accelerated time frame while ensuring no adverse impacts to business as usual operations.
More crucially, we were able to improve visibility and control for the client over its inventory through utilising our teams’ expertise on changes to British standards as well as how specific products and fastening systems have migrated over to the ISO or DIN standards.
Our project team was particularly proud that, as a direct result of this project, our client was able to greatly enhance its quality regime; to the extent that they only observed a single rejection in the following 18 months.