Case Study: Custom Fixings for Wind Turbines and Towers
Industry:
Energy
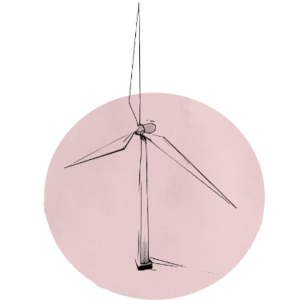
Project Summary
The client, a global leader in the automotive sector, decided to build two large wind turbines to increase their clean energy capacity and in doing so, facilitate the implementation of ESG goals.
When completing the site survey for the project, the client's installation team discovered that new bolting would be required for the build as the original bolts could not be reused.
Obviously this presented an issue as sourcing custom-made, high-grade fastenings in an accelerated time frame can prove difficult.
This is when we became involved in the project.
Method
The first thing we did was send a team to the site to understand the technical requirements and detail a scope of work.
Our team identified the bolts, nuts, spacers and washers required. The requisite parts included; large diameter high grade alloy steel bolting, high grade nuts, and hardened washers and spacers.
We presented a quote which factored-in expedited delivery to meet the demanding client-led timescales.
The quote was accepted and we managed to provide the full breadth of product within seven working days. (This job would typically have taken three to four week without factoring expedited delivery).
RESULT
A resounding success.
Our bespoke procurement solution and agile practices enabled our client to avoid operational and financial risk on a high profile project. Satisfied with the outcomes, our client asked us to collaborate on the implementation of additional wind turbines to enlarge the innovative scheme.