Case Study: Streamlining Stock Delivery with Kanban System
Industry:
Manufacturing
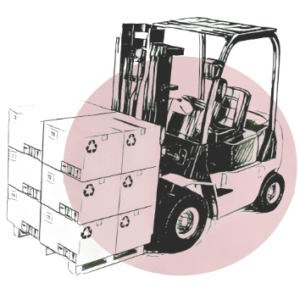
Introduction
Catering to major accounts with exceptionally high stock turnover rates demands a tailored approach that ensures seamless stock delivery and efficient inventory management. With over 26 years of experience in serving such clientele, our company has honed a specialized solution—the Kanban system—to meet their unique requirements. This case study highlights how our Kanban solution has transformed stock delivery processes for major accounts with high stock turnover, enhancing operational agility and customer satisfaction.
The Challenge:
Over the years, our company has encountered various challenges in stock delivery and inventory management. Traditional methods often resulted in stockouts, excess inventory, and operational inefficiencies. To overcome these challenges and maintain our competitive edge, we sought a solution that would streamline our stock delivery process and empower our customers with greater control over their inventory levels.
The Solution
Drawing on our years of experience and industry expertise, we embraced the Kanban system—a proven methodology derived from Japanese manufacturing principles. By leveraging the principles of visual cues and just-in-time inventory management, we transformed our stock delivery process to better serve the needs of our customers.
Key Features of Our Kanban System:
1. Inventory Savings: With our extensive experience and refined Kanban system, customers experienced significant savings in inventory costs. Real-time visibility into inventory levels allowed for precise control, minimising excess stock and reducing carrying costs.
2. Elimination of Purchase Orders: Our 26 years of experience with the Kanban system enabled us to seamlessly integrate it into our operations, eliminating the need for cumbersome purchase orders. This streamlined approach accelerated order processing and reduced administrative overhead.
3. Just-in-Time Delivery: Leveraging our expertise, we fine-tuned our Kanban system to facilitate just-in-time delivery, ensuring that stock was replenished precisely when needed. This minimized the risk of stockouts and optimized inventory levels, resulting in improved operational efficiency.
4. Tailored Delivery Frequencies: Building on our extensive experience, we offered customers various delivery frequencies tailored to their specific requirements. Whether customers needed deliveries twice a day, once a week, or once a month, our flexible Kanban system could accommodate their needs, providing greater control over stock levels.
Benefits for Our Customers:
Controlled Stock Levels: Our 26 years of experience with the Kanban system empowered customers to maintain optimal stock levels, minimising excess inventory and ensuring product availability.
Improved Efficiency: By streamlining stock delivery processes, customers experienced increased operational efficiency, reduced downtime, and enhanced productivity.
Cost Savings: Through effective inventory management and just-in-time delivery, customers realized significant cost savings, including lower inventory costs and minimized stockouts.
Enhanced Satisfaction: Our extensive experience with the Kanban system translated into reliable and timely stock deliveries, fostering greater customer satisfaction and loyalty.
Conclusion
In conclusion, our 26 years of experience combined with the Kanban system have revolutionized our stock delivery process, enabling us to meet the evolving needs of our customers with precision and efficiency. By leveraging the principles of just-in-time inventory management and tailored delivery frequencies, we have enhanced customer satisfaction, reduced costs, and solidified our position as a trusted partner in inventory management. As we continue to build on our experience and refine our processes, we remain committed to delivering exceptional value and service to our customers.
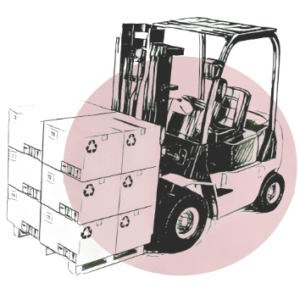